Hétköznapjaink elképzelhetetlenek megbízható személyautók nélkül. De vajon mennyi szakértelemnek kell összpontosulnia, hány százezer tesztciklusnak kell végigpörögnie, hogy a több millió indítás és leállítás, gázadás és fékezés olyan zökkenőmentesen történhessen, ahogy azt elvárjuk? Természetes, hogy bele sem gondolunk, hiszen nem látjuk magunk előtt az akusztikai mérnököt, aki a vizsgálókabinban a legmagasabb szintű technológiával ellenőrzi a karosszéria kívánt csendességét, ahogy azzal sem vagyunk tisztában, hogy autónk motorjának ideális működése a monitor előtt sok-sok ezer munkaórát eltöltő szimulációs mérnökök munkájának gyümölcse. Most azonban betekinthetünk a kulisszák mögé. Műszaki Fejlesztésünkön – amely az AUDI AG harmadik legnagyobb fejlesztőközpontja – már a reggeli kávé mellett szapora egyeztetés zajlik. Fotósok és videósok pontosítják még egyszer az előre megbeszélt forgatási helyszíneket Gyetván Csaba televíziós műsorvezetővel, a „Hogyan készül?” tematikájú videók házigazdájával. A vlogger-műsorvezető és stábja ugyanis a Discovery Channelre készülő „Made in Gyetván Csabával” széria következő epizódjait forgatja az Audi-gyárban zajló műszaki fejlesztésről. Hétfő reggel kilencre minden és mindenki kész, foroghat a kamera!
Csendet kérünk!
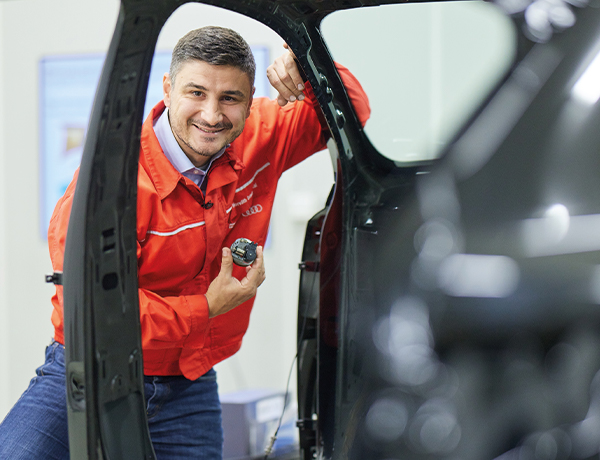
A Járműfejlesztésen kezdünk: szilárdsági vizsgálók és görgős vizsgálópadok között közelítjük meg első állomásunkat, az akusztikus termet. Kívülről úgy fest, mint egy hatalmas trezor: félméteres vastagságú ajtó zárja a helyiséget, amelyben akusztikus elnyelő szigetelőanyag akadályozza meg, hogy a hanghullámok visszaverődjenek a falakról. A szellőzőrendszer ugyancsak zajszigetelt, a termet pedig alacsony zajszintű kipufogógáz-elszívó rendszerrel is felszerelték arra az esetre, ha járó motoros tesztre kerülne sor. A cél, melyért itt dolgoznak, hogy csökkentsék az autók működése közben keletkező zajok erősségét, elzárva azokat az utastértől. „Ha nem vagyunk ügyesek, a karosszéria egy jól működő hangszóró” – magyarázza dr. Horváth István Antal akusztikai fejlesztőmérnök egy „nyers” Q3 Sportback karosszériája mellett állva, miközben elemzi a karosszériára irányított lézeres szkenner által küldött adatokat, amelyekből összeáll a lengéskép. Időnként olyan hangok szólalnak meg a teremben, mint Andrej Tarkovszkij Solaris című klasszikusában, máskor altatódal csendül fel, István pedig minden adatot rögzít.
"Ha nem vagyunk ügyesek, a karosszéria egy jól működő hangszóró."
Vigyázz, centrifuga indul!
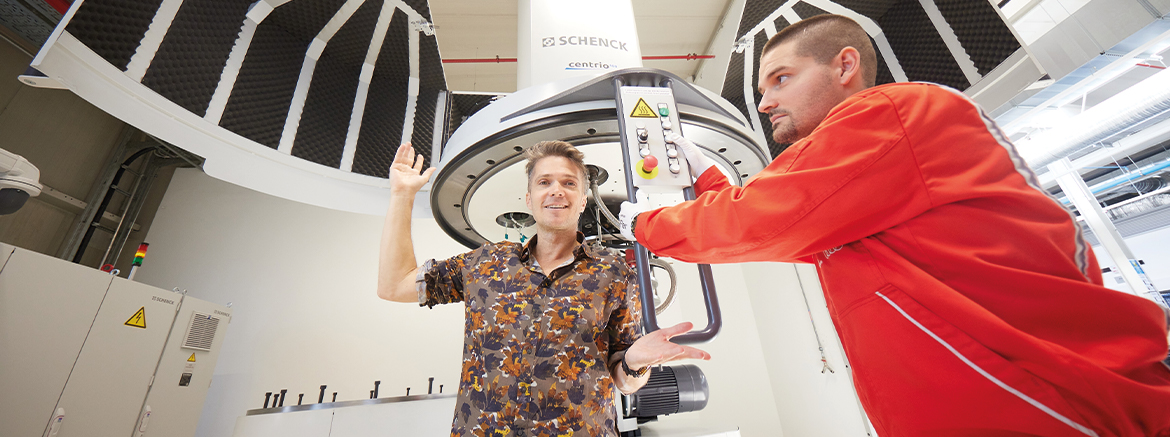
A fojtogató csendből visszatérünk a hangok világába, az akusztikus teremtől pár lépésre lévő forgórészvizsgáló centrifugák (SPS) mellé. Az egyenként 4-5 méter magas gépek a rotor perdületvizsgálatára, ciklusvizsgálatára és tartósságvizsgálatára szolgálnak. A centrifugákban a különböző élethelyzetekre adott reakciókat, de akár a teljes élettartam alatti terhelést is szimulálják, megnézik az elektromos autók villanymotorjának lelkét jelentő rotor szilárdsági viselkedését. A vizsgálati módszerekbe Dobos Mátyás fejlesztőmérnök avat be minket. „A perdületvizsgálatkor a rotor alakváltozását mérjük. A centrifugában üzemi körülményeket idézünk elő, majd szenzorokkal másodpercenként 180 ezer mérési ponton rögzítünk adatokat. A ciklusvizsgálat más: ebben a fázisban két héten át napi 24 órán keresztül pörgetjük a rotort, ahol a vevői használatot jóval meghaladó fordulatokat érünk el. Arra vagyunk kíváncsiak, hogyan reagál a rotor extrém terhelés alatt. A tartósságvizsgálat lényege pedig az, hogy tönkremenetelig terheljünk.” Gondoljunk csak bele, milyen szélsőséges körülmények szükségesek ahhoz, hogy egy többkilós acéltest széttörjön! Miután rögzítik a rotort, a centrifugát lezárják. Ahogy növelik a fordulatszámot, a fixált egység körül elhelyezett kerámialapokat 130-180 fokra hevítik fel, míg végül a rotor extrém magas fordulatszámon forog, és a vákuumban egyszer csak megadja magát. Ebben a pillanatban a rendszer nitrogént juttat a centrifugába, hogy ne keletkezzen szikra. A centrifuga belső rétegét egymástól néhány centire három féltonnás acélgyűrű védi, töréskor a legbelsőbe valósággal beépülnek a rotordarabok. „Olyan erejű a becsapódásuk, hogy az első acélgyűrű képes elmozdulni a helyéről. A mérések szerint van olyan rotordarab, amely 1 mach sebességgel, vagyis hangsebességgel ütközik a gyűrűnek” – érzékelteti Mátyás az odabent dolgozó erők nagyságát. A két centrifuga komoly előrelépés a fejlesztésben: ilyen jellegű vizsgálatokat a Volkswagen Konszern eddig csak külső cégek bevonásával tudott elvégezni, de ezek által már házon belül van a technika. Ugyanakkor fontos megemlíteni, hogy ilyen folyamat üzemi körülmények között nem játszódhat le, hiszen az autók motorja az ügyfelek kezei között ennél lényegesen alacsonyabb fordulatszám-tartományban működik.
Bírja a rendszer?
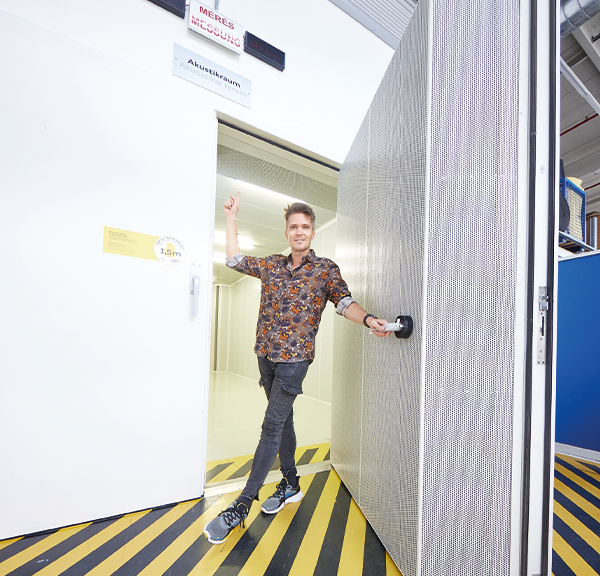
Következő helyszínünk a görgős fékpad: egy terembe lépve az alábbi látvány fogad: három szakember a monitoron egy szemrevaló Porschét figyel. A „tesztalany” a járművizsgáló görgős fékpadján pihen, miközben két hatalmas ventilátor mesterséges menetszelet gerjeszt körülötte. Mintha az autó hegyek és völgyek között haladna, a sebességváltozás pedig a városi dugókban lelassuló és felgyorsuló tempót idézi. A 160 tonnás fékpad a föld alatt kialakított acélrugókon fekszik, ugyanitt kaptak helyet a ventilátort beindító villanymotorok is – ez utóbbiak képesek előidézni a 130 km/h sebességű menetszelet. A vizsgálat célja: eltérő terhelési fokozatok alatt, néha maximális sebesség (280 km/h) mellett ellenőrizni a kipufogórendszer és az új alkatrészek működését, miközben bizonyos darabokat nyúlásmérő bélyegekkel és gyorsulásmérőkkel látnak el. A mérnökök azt is figyelik, milyen hanghatások és rezgések jelentkeznek menetközben. A falat itt is zajvédő borítás fedi, hiszen akusztikai mérésekre is sor kerül a görgős fékpadon, ahol órákon, sőt akár heteken át figyelik a jármű gördülési zajait.
"A mérnökök azt is figyelik, milyen hanghatások és rezgések jelentkeznek menetközben."
Motorvezérlés? Rendben.
A HiL laborban (Hardware in the Loop) Takács Gábor Ferenc és Kajcsos László fogad bennünket egy szerverszobára emlékeztető környezetben. Ők azok, akik gépi segítség igénybevételével a fejlesztés korai fázisában tesztelik a motorvezérlés teljes hálózatba való bekapcsolását. Ez lehetővé teszi, hogy már a valós járművizsgálatokat megelőzően információkat gyűjtsenek, melyeket a további fejlesztéshez is felhasználnak. „Az Audi által gyártott sokféle járművön nem lenne gazdaságos az üzemi vizsgálat, ezért a szakemberek olyan berendezéseket fejlesztettek ki, amelyeken minden belső égésű és elektromos motor elektronikáját lehet tesztelni. Ezek a gépek szenzoros és terheléses szimulációt is végeznek, ahogy a vezérlőegységgel való összekapcsolódást is vizsgálják” – fejtették ki a szimulációs mérnökök. Érdekesség, hogy ugyanezt a technológiát használják a repülőiparban és az űrkutatásban A nap végéhez érve csak úgy zsong a fejünk a rengeteg információtól és impulzustól, de alig várjuk a másnapi folytatást, amikorra még töményebb programot és hasonló érdekességeket ígér a Műszaki Fejlesztés Járműhajtás Fejlesztés csapata.
Így születnek az erőforrások
Második napunkat a Járműhajtás Fejlesztés irodaépületében kezdjük Doór András, az akusztikus csapat szakmai koordinátora társaságában, akivel gyorsan a lényegre térünk: „Az AUDI AG megalkotja a koncepciót, mi itt, Győrben készre fejlesztjük, és legyártjuk a járműhajtást, a folyamat vége pedig a késztermék.” Miközben beszélgetünk, átsétálunk az aulán, ahol egy 3,0 literes Audi S5 TFSI motorja mellett haladunk el. Nehezünkre esik nem lecövekelni mellette, legszívesebben órákon át gyönyörködnénk benne, de muszáj haladni, sűrű a program. A konstrukciós mérnökségen, ahova gyorsan át is érünk, az alkatrészek háromdimenziós környezetben zajló tervezése történik. Az itt dolgozók azonban nemcsak terveznek, hanem végig is követik az adott alkatrész életútját, hiszen tartaniuk kell a kapcsolatot a tesztmérnökökkel, a gyártástervezéssel, beszerzéssel, kontrollinggal, minőségbiztosítással, logisztikával, valamint az illetékes gyártóterülettel is. A stábot Michl Dániel várja, aki konstruktőrként villamoshajtások tervezésével foglalkozik. Érkezésünkkor épp egy e-tron SUV hajtását vizsgálja a monitoron. Riporterünk, Csaba kérdésére mesélni kezd a munkájára jellemző folyamatokról. „Alapvetően tervezéssel foglalkozunk, de hogy mi az aktuális feladatunk, az attól függ, miről van szó… Egy projekt kezdődhet egy már meglévő belső égésű motor vagy elektromos hajtás továbbfejlesztésével, vagy indulhat a nulláról. Ebben az esetben nem az előző generációk modelljét fejlesztjük, hanem egy teljesen új koncepciót. A második esetben természetesen a korábban szerzett ismereteket, tapasztalatokat is felhasználjuk. A megrendelők számára továbbra is kiemelten fontos az autó teljesítménye, (költség)hatékonysága, elektromos autók esetén pedig természetesen a hatótáv” – sorolja. A csapat így ezen tényezőket figyelembe véve tervez.
Tisztára, mint a moziban!
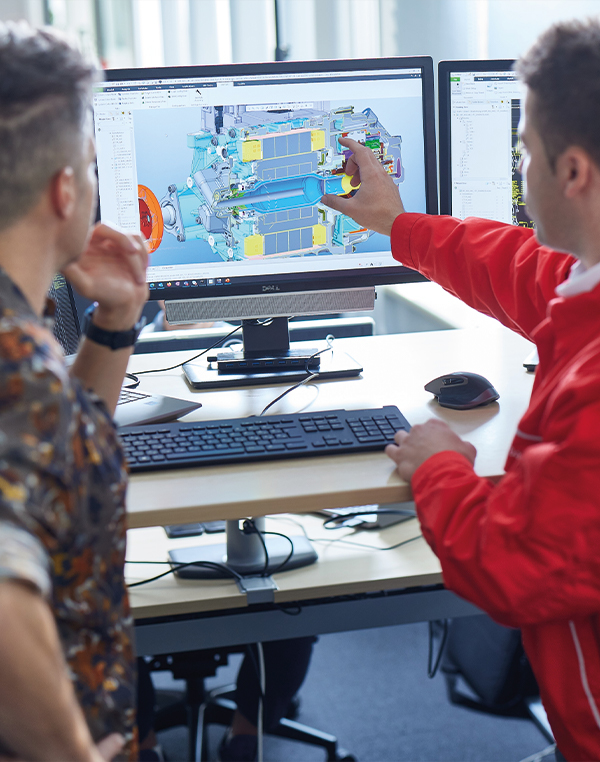
A Műszaki Fejlesztésről egy kis kitérőt téve látogatásunkat követően Dániel a villamoshajtás-szereldébe is elkísér minket, amely laikus szemmel nézve az egyik leglátványosabb helyszín. Belépve rabul ejt bennünket a Star Wars-lényeket idéző, vezető nélküli elektromos szállító járművek (FTF – Fahrerloses Transportfahrzeug) látványa, melyekből összesen harminchat közlekedik az üzemben tökéletesen önállóan, emberi felügyelet nélkül. Kisvártatva „össze is ismertetnek” minket velük. A csapatunkat fogadó Józsa Attila projektmenedzsertől közben megtudjuk, hogy – az FTFeken kívül – 330–340 kolléga dolgozik a szereldében, három műszakban. Itt készül a státor, vagyis az e-tron SUV-ba épített villamos hajtás állórésze, naponta nem kevesebb mint 530 darab. A következő lépcsőben ebbe az állórészbe szerelik be a rotort, a csapágyakat, a tömítéseket és az egyéb szükséges alkatrészeket, a váltót, majd a kész erőforrás megy a tesztpadra, végül pedig Brüsszelbe, ahol bekerül az autóba. De kanyarodjunk csak vissza a „kutyának” becézett szállítókocsikhoz, amelyek nélkül ma már nem lenne gördülékeny a gyártás! A gyártószigetek között ők mozgatják az alkatrészeket és a hajtás részeit, és ha az útjukba kerülünk, ránk szólnak. Egy töltéssel három-négy órán át képesek közlekedni kijelölt sávjaikban, majd maguktól rákapcsolódnak a töltőre. A szereldében működő valamennyi géptől egy központi programhoz futnak be az információk, amely a beérkező inputok alapján utasítja a szállító járműveket, hogy melyik gyártószigethez menjenek legközelebb. A találkozásért különösen hálásak vagyunk, mivel ilyen technológiát más autógyárban nem nagyon láthatnánk.
"A konstrukciós mérnökségen az alkatrészek háromdimenziós környezetben zajló tervezése történik."
Tesztek helyett szimuláció
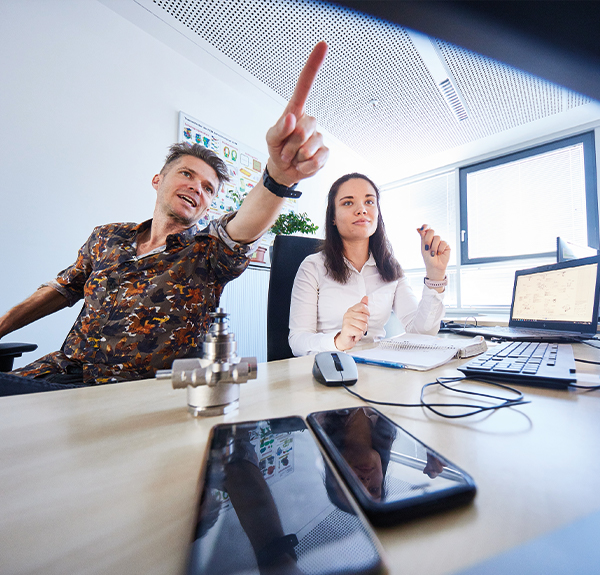
Ocsúdni sincs időnk, pár perc elteltével már az egyik szimulációs mérnök monitorja előtt állunk: Sipos Beatrix numerikus szimulációkat végez a valós használat során felmerülő terhelésekre alapozva. Csapatával olyan kérdésekre keresik a választ, hogy bizonyos terhelés mellett eltörik-e egy alkatrész. „Ezzel a munkával nagyon sok erőforrást, időt és pénzt tudunk megtakarítani” – mondja, és nem túloz. A numerikus szimuláció kiváltja a fékpadi és járműves tesztek egy részét, hiszen előre megmondja az egyes alkatrészek várható élettartamát.
Újabb zajpróba
Viszont, ha van helyszín, ahol nem lehet megspórolni a tesztelést, az az akusztikus fékpad. Rőfös-Horváth Viktor kísérleti mérnök és korábbi ismerősünk, Doór András egy zajszigetelt teremben, egy Lamborghini-motor mellett magyarázza el a teszt lényegét. Itt gyorsulásérzékelők és mikrofonok segítségével órákon át tesztelik a járó motor zajszintjét és rezgéseit, majd a változatos üzemi körülmények között megszülető eredmények alapján a csapat meghatározza, hogy a gyártósorról érkező vagy épp egy működő autóból kiszerelt motor akusztikailag rendben van-e, és ha nem, melyik alkatrészével van probléma.
Extrém körülmények
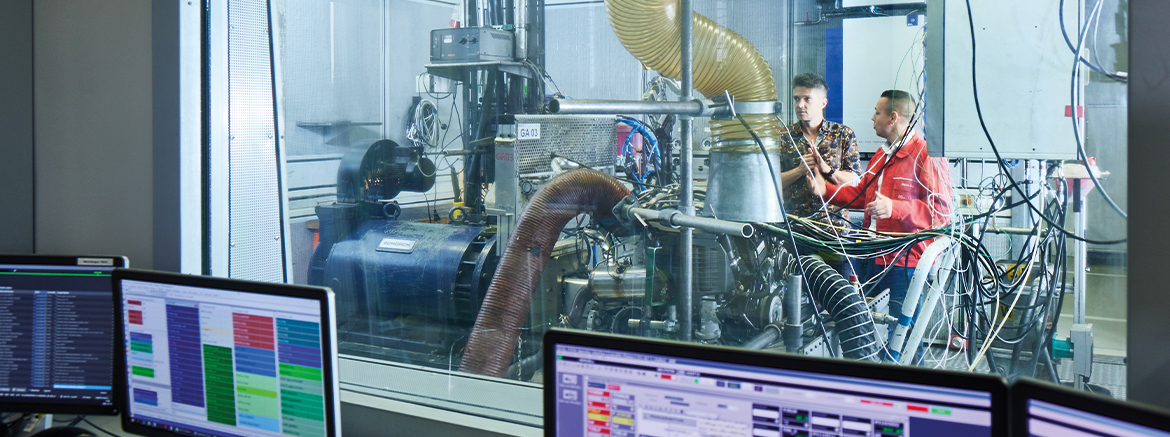
Gyárlátogatásunk és a forgatási helyszínek utolsó állomása szintén a tesztcentrumban található. A hosszú távú vizsgálatok helyszíne ez, ahol az egymás után sorakozó kabinokban a forróságot jéghideg váltja fel: a 14-es számú klímakabinban +40 és –40 Celsius-fok között végzik a hibrid hajtásláncban használt erőforrások klimatikus tesztjeit. Mi –28 fokba érkezünk Balics Ákos fejlesztőmérnök kíséretében, akitől megtudjuk: az északi országokban sokkal nagyobb az igény a hibrid erőforrásokra, többek közt ezért végzik ilyen hőmérsékleten a teszteket. Mivel a hibrid járművekben sűrűn állítjuk le és indítjuk újra a motort, szélsőséges tesztekre van szükség a hőmérsékleti és egyéb paraméterek gyakori változtatása mellett. A kabinban néhány másodpercenként indítja újra és állítja le a hajtást egy motor – napi 24 órán keresztül. Van olyan motor, amely tizenkét hét alatt 100 ezer kilométert pörög. „Ez az egyik legösszetettebb, úgynevezett start-stop teszt. Napi háromezer start-stop ciklust végez a rendszer, a vizsgálat kétszázötvenezer ciklusnál áll le. Közben cseréljük persze az olaj- és levegőszűrőt, a gyújtógyertyákat, és figyeljük a motortulajdonságokat, a frekvenciákat, a motorvezérlő és az alkatrészek működését. A járatás során felmerülő problémákra azonnal reagálnunk kell. Nincs két egyforma munkanap, de éppen ez adja a varázsát a szakmánknak” – hallgatjuk elképedve a szakembert a tesztpad monitorja előtt.
Kétnapos felfedezőutunk végén a látottakat és hallottakat összegezve elmondhatjuk: az Audi Hungaria nem lassít, sőt! A következő évek során a vállalat két számjegyű eurómilliós összeget fordít a Műszaki Fejlesztésre. E beruházás keretében egy újabb fékpadot telepítenek az elektromos tengelyhajtások és a hozzájuk tartozó áttételek fejlesztéséhez, valamint korszerűsítik a meglévő fékpadi infrastruktúrát, hogy még nagyobb mértékben járuljanak hozzá a mobilitás jövőjéhez – …Győrből a világnak.