Nincs olyan dolgozó, aki ne kerülne kapcsolatba vele – mint megtudtam – a járműgyárban nincs olyan munkaütem (takt), ahol a soron érkező Audi TT vagy Audi TT Roadsterrel ne kelljen foglalkozni – legalább egy simítás, simogatás erejéig. De ne szaladjunk előre, menjünk a sor elejére.
A győri Audi-gyár hatalmas, nem hiába ez a világ legnagyobb motorgyára. Az Audi TT összes motorja is helyben készült, sőt már azokban az időkben is, amikor az összeszerelés nem minden fázisa történt itt. 2013 óta azonban szinte minden porcikája győri a TT-nek – persze van jó pár alkatrész, ami beszállítóktól érkezik, de még azok között is vannak győriek és Győr-Moson-Sopron vármegyeiek. A motorgyártással, gyártástervezéssel, fejlesztéssel, minőségellenőrzéssel, teszteléssel ezúttal nem foglalkozunk, csak a fő sodrásban haladunk. Négy területet látogatunk meg: présüzem, karosszériaüzem, lakkozó és járműszerelde. A tapasztalatokról és az élményekről négy cikkben számolunk be. Tartsatok velünk, izgalmas lesz!
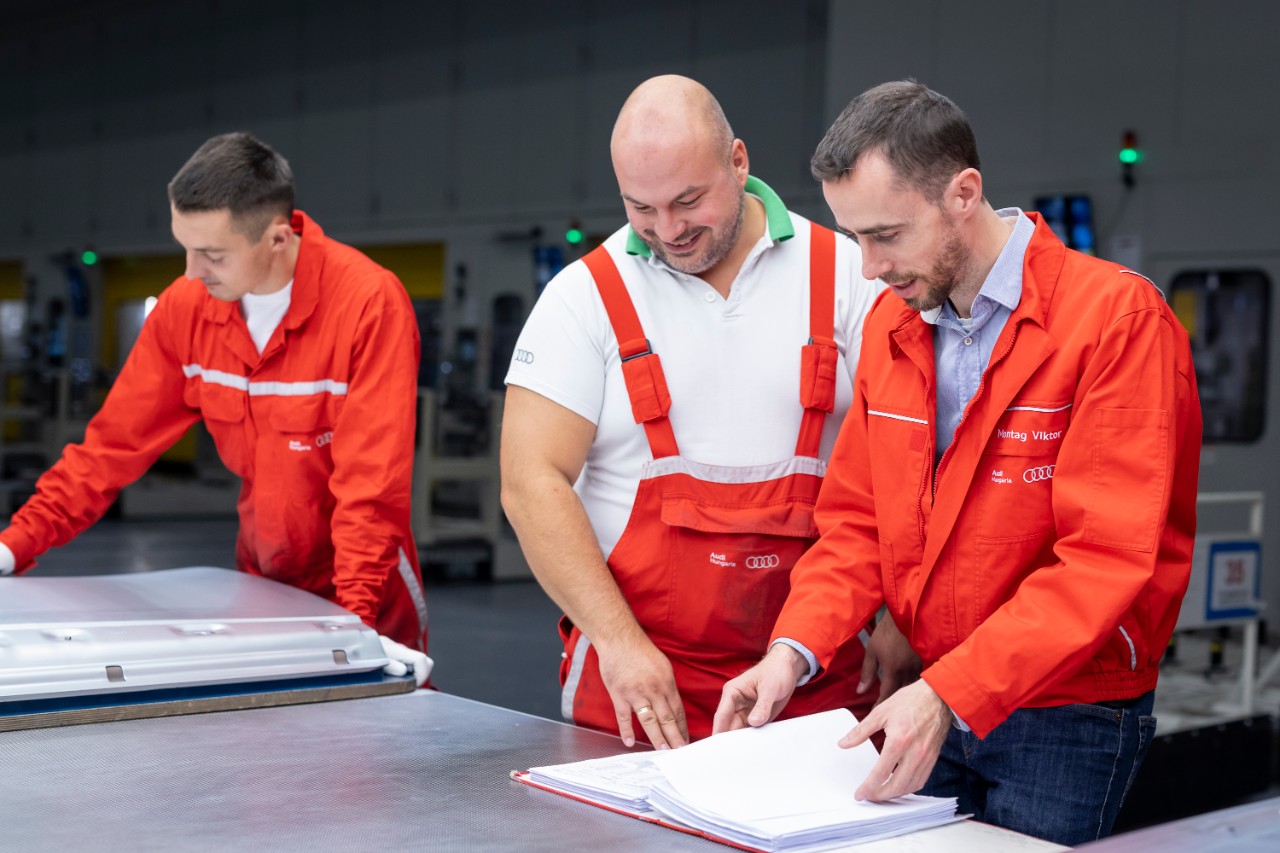
Présüzem: Ahol a lemezből alkatrész lesz
Az 5-9 tonna tömegű alumínium- és legfeljebb 33 tonna tömegű acéltekercsek vasúton érkeznek egy külső, dorogi raktárba, ahonnét speciális, bölcsős teherautóval szállítják őket a gyárba – osztja meg a teremtés első mozzanatait Montag Viktor, a présüzem termeléstervezője. A daruval leemelt tekercsek bekerülnek egy köztes munkaterületre, ahol a vágást követően három ágon mennek tovább. Egy részüket Pozsonyba szállítják, ott egy győrihez hasonló présgéppel dolgozzák fel a lemezeket, kap ezekből a szerszámgyár és természetesen a győri présüzem, ahol az Audi TT sportkocsik élete elkezdődik. A kipréselt elemeket készáru raktárban tárolják, a karosszériagyártás pedig a saját igényei szerint veszi ki a megfelelő alkatrészt. „A TT esetében többnyire alumíniumot dolgozunk fel, nagyjából 80 százalék az alumínium aránya. Minden, ami kívül van a kocsin az alumínium, ami acél, az többnyire belül található: ilyen a padlólemez, a kerékjáratok, bizonyos szerkezeti elemek”, avat be a részletekbe Montag Viktor.
Hangos a présüzem, főleg, ha a két Schuler gép közelébe érünk: a vágógép 70, a prés nagyjából 25 millió löketet teljesített eddigi élete során, 2013-ban kerültek ide. Előtte Ingolstadtból érkeztek a lakkozott karosszériák, akkor még a TT első, majd második generációjához. A harmadik generáció számára, amely 2014-ben debütált, már a győri présüzemben készültek a karosszériaelemek.
A présüzemben a fókusz az egyensúlyozáson van: legyen megfelelő minőségű a termék, minél kisebb legyen a levágott hulladék aránya. A bejövő anyagmennyiség mintegy 40 ezer tonna, aminek mintegy fele első körben technológiai hulladék lesz. Ezt természetesen újra felhasználják, az Aluminium Closed Loop keretében a vállalatnál megvalósul az alumínium zárt körforgása, így az értékes alapanyag azonos minőségben ismét visszakerül a körforgásba.
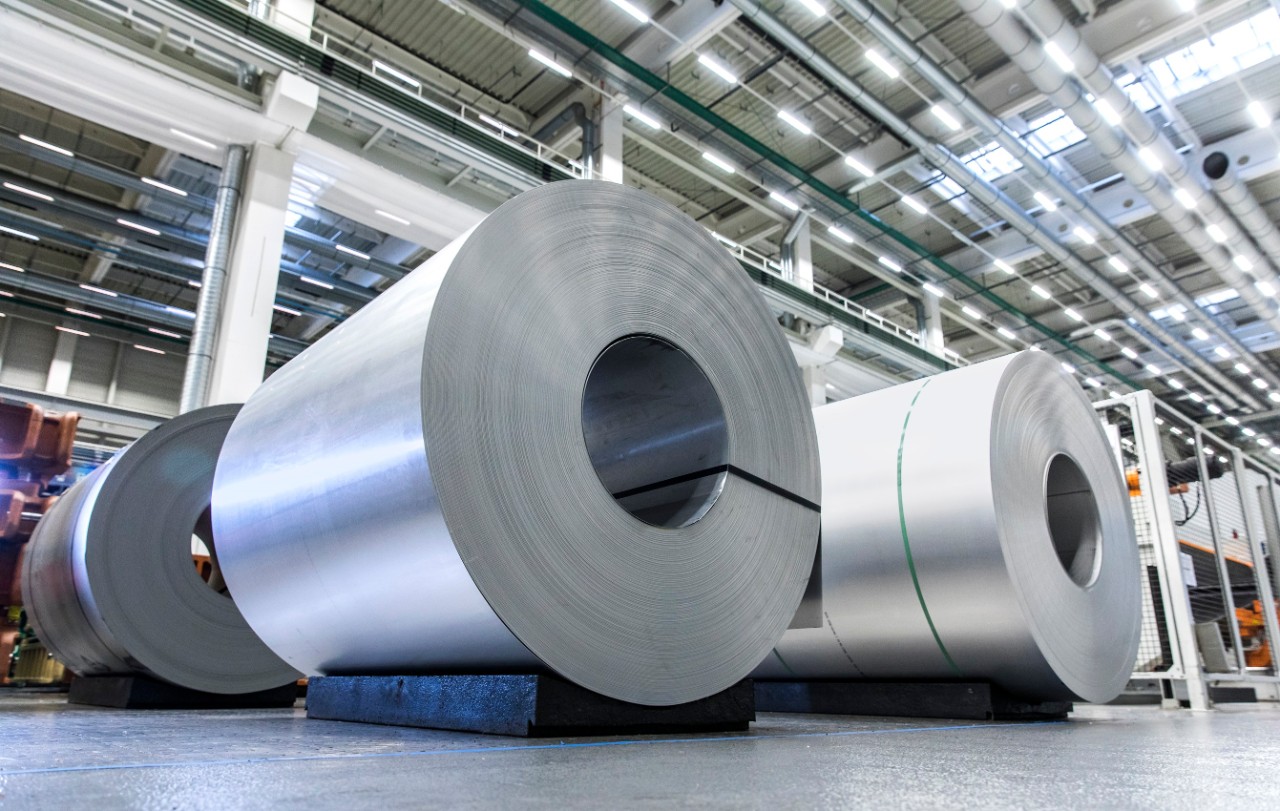
A présüzemben, ahol hozzávetőlegesen 180-an dolgoznak, éppen kerékjáratok, majd oldalfalak készülnek a TT-hez, a nagy daru mellett 8 tonna teherbírású targoncákkal folyik az előkészítő munka. Elmegyünk a lemezgödör mellett, ahol a tekercsek folytonos mozgásával kontrasztban szakaszosan, kiegyengetve biztosítják az acél-, vagy az alumínium lemezek zavartalan vágását és áramlását. 106 TT présszerszám- (alkatrészenként mélyhúzás, vágás és lyukasztás, egy leütésre akár több alkatrész gyártása is történhet) található a győri üzemben, mindenre megvan a megfelelő szerszám. A szerszámok egy részét a szomszédos szerszámgyárban készítik. Ezekből rengeteg van, a TT búcsúzását követően jó részüket anyagában újrahasznosítják, de néhány szerszám utángyártása tovább folytatódik. Ennek során még évekig préselik a TT alkatrészeket a szervizek számára. Persze, nem ilyen darabszámban...
Fölöttünk tonnák, körülöttünk tonnák
Megérkezünk a préshez, összereje 81.000 kilonewton, azaz 8100 tonnás. Robotizált az alkatrésztranszfer, ám az előszerelésben emberek is dolgoznak, a szerszámokat ők daruzzák fel. Fölöttünk százezer eurós és 15-20-40 tonnás szerszámok húznak el, távirányítóval vezérli egy munkatárs, mint egy játékkonzolt.
A présben a lemezek pozícionálása látványos munkafázis: egy robotpár előkészíti, hogy a lemez teljesen pontosan érkezzen meg a mélyhúzáshoz. Jellegzetes pontokat figyel, jellemzően sarokpontokat. Montag Viktor közben sorolja az adatokat: a fejprés 2100 tonnás, ott történik a formázás, a követőprések 1200 tonnások.
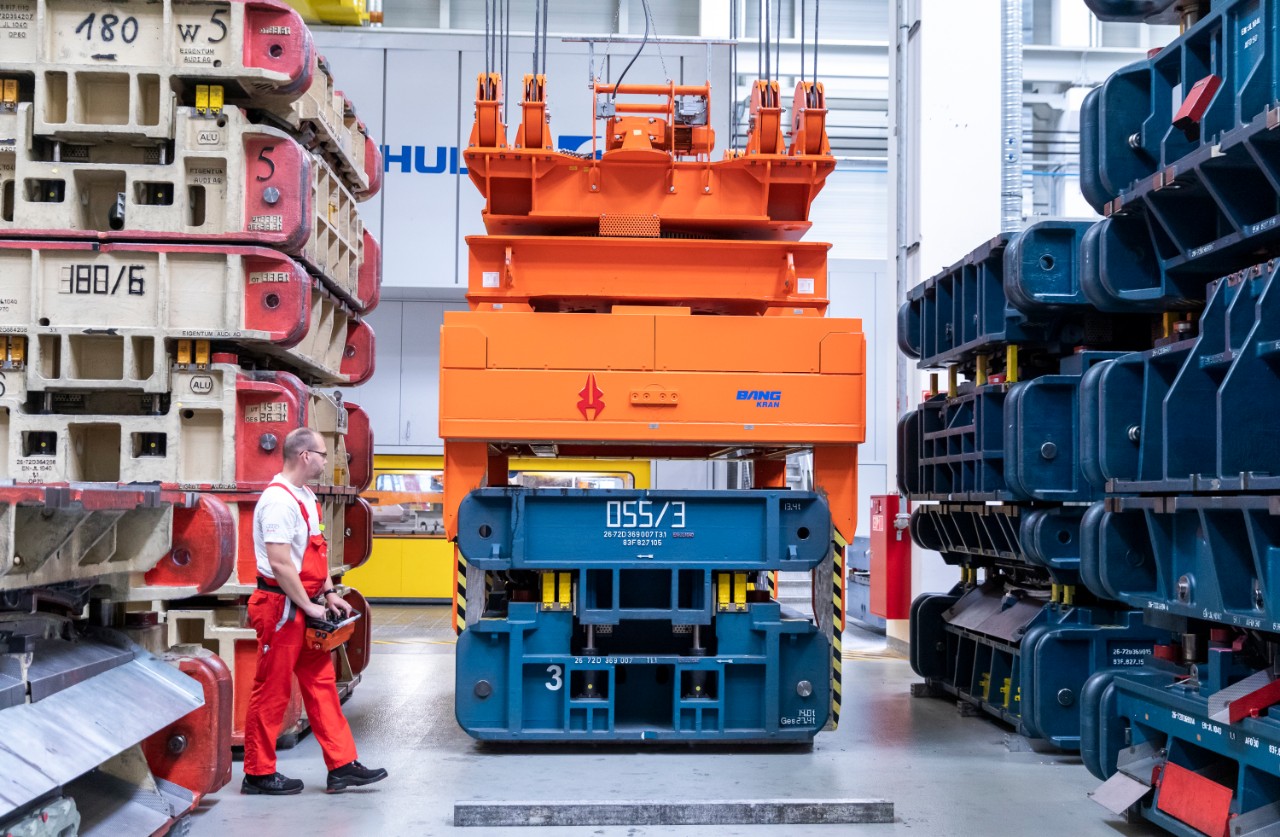
A folyamat végén megnézünk néhány alkatrészt. De nem egyedül, 7-8 dolgozó a két szalag mellett (párban készül az alkatrészek zöme) szemrevételezéses gyorsvizsgálatot tart, egyszámjegyű másodperc az idő, ami alatt észre kell venni a hibát. Egy másik kolléga egy-egy órás ciklusban mélyebben is megvizsgálja (óránként vagy 400 darabonként) – lehúzókővel lehúzza a felületet, hogy lássa a felületi hibákat, megszámolja a furatokat – valamint ellenőrzi a többi minőségi ismérvet. A minőségellenőrzés tehát a TT gyártása közben is – mondhatni – folyamatos. Van egy, a présüzemi dolgozóktól független minőségbiztosítási kontroll is – termelésenként egy alkatrészt vesznek ki és alaposan megvizsgálják. Ezt már a minőségbiztosítás végzi itt helyben, a présüzemben. Ha hiba van, akkor azonnal meg kell keresni a rossz termékeket, fel kell tárni a hiba okát és ki kell azt javítani.
Pehelykönnyű alkatrészek
A kész termékek és mintadarabok között vezet az utunk: acél kerékdobok külső és belső elemeit nézzük, ez itt arrébb padlólemez. „Amott az acélnak van egy kis narancsbőrössége – ennél az alkatrésznél ez nem gond, de az alumínium sárvédőnél, ami látszik, na ott tökéletesnek kell lennie a kivitelezésnek”, avat be a titkokba Viktor. Az alkatrész pehelykönnyű, egy ujjal megemelem. A Roadster első szélvédőkerete is könnyű, csak épp gyártani nem az. A fő nehézséget az jelenti, hogy egy tekercsből nagyon sok szélvédőkeret jön ki, az alumínium feldolgozása pedig az idő előrehaladtával egyre nehezebbé válik. Egy tekercs akár több mint egy évig is kitarthat, és külön vizsgálni kell az anyagot annak további felhasználhatóságára. Összehasonlításképp: egy oldalfal esetében egyszerre levágunk egy tekercset, a lemezek, illetve préselemek pedig néhány hét alatt elfogynak. Így komoly fejtörést okoz, hogyan gazdálkodjuk ki”, mondja Viktor. Megoldás: vegyenek több Roadstert, emberek! – de ezt már én teszem hozzá a présüzem kijáratánál, ahol újra hallunk – a présgépek ugyanis elég hangosak.
Kis darabszám és alumínium – ez TT sajátosság. Megtudjuk azt is, hogy tekercsformában 2-3 hónapot tölt el az alapanyag, a tekercspufferben egy napot, a vágógépen egy órát, lemezként néhány napot, ahhoz, hogy majd a présen eltöltött öt perc után alkatrészként távozzék. A folyamat végén ismerős formákat látok. Hogy készül az oldalfal? „A vágógépen kivágjuk a tágulási nyílásokat és a sarkokat, lényegében egy nagyon tág körvonalat kapunk, következik a mélyhúzás, ahol nem vágunk semmit. Ezt követően, miután a forma nagyja elkészült, szakaszosan vágjuk, majd utánformázzuk, élesítjük a markáns élek rádiuszát, előkészítjük a tanknyílást, a kerékjáratokat, majd további kis vágásokat, formázásokat végzünk, furatokat, lyukakat vágunk. Mindezt nem lehet egy operációba sűríteni, szét kell választani, legalábbis nálunk. A dizájn áll szemben a szerszám konstrukciósköltségekkel”, magyarázza Viktor.
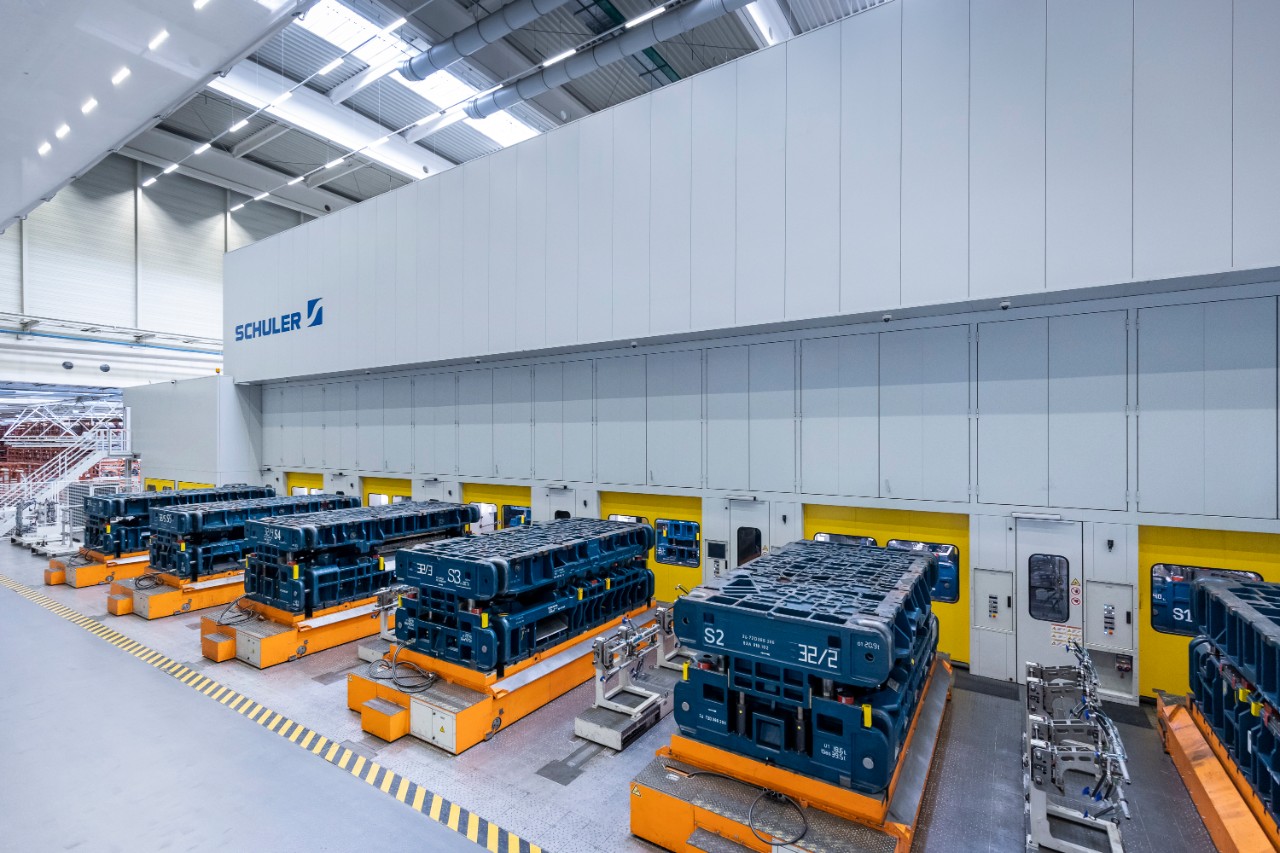
De természetesen a TT-re nem lehet csupán racionálisan, a számok alapján tekinteni, itt az érzelmek is jelentős szerepet kapnak. Ahogy valamennyi Audi Hungariás munkatárs, így Viktor is nagyon sajnálja, hogy el kell köszönni ettől a legendás modelltől. „Ugyan gyártási szempontból okoz számunkra kihívásokat a TT, de mindezek ellenére nagyon szeretjük, hiszen a miénk, a harmadik generációja pedig ízig-vérig győri. Büszkén gyártjuk egészen az utolsó darabig”, zárja a beszélgetést Viktor.
Sorozatunk következő részében a karosszériaüzembe látogatunk.